pp板材熱氣焊接工藝參數(shù)和材料
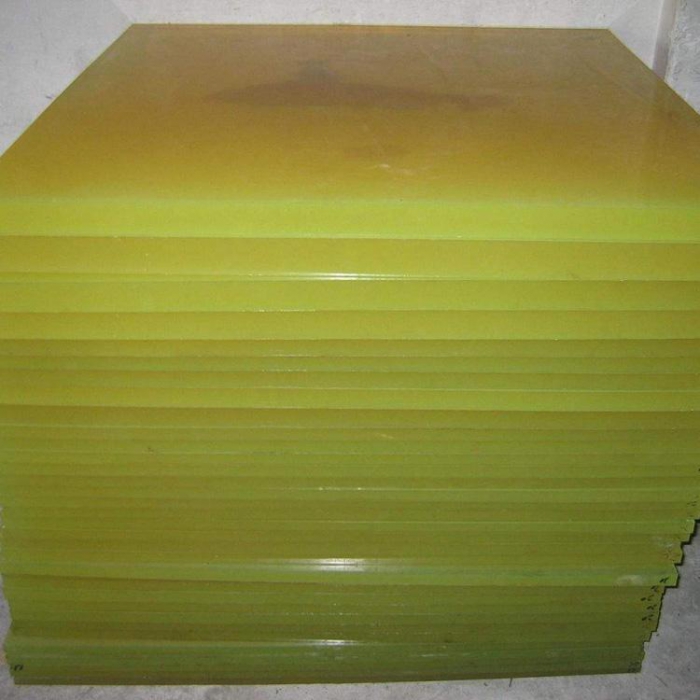
pp板材熱氣焊接工藝參數(shù)(parameter)和材料
大多數(shù)PP板材可以采用熱氣焊。煤倉(cāng)襯板超高分子量聚乙烯的超高分子量的含義是它不會(huì)融化并向液體一樣流動(dòng),因而加工方法由粉末金屬技術(shù)衍生。吊車支腿墊板超高分子量是這種聚合物與眾不同的特質(zhì),其具有300至600萬的分子量,而高密度聚乙烯樹脂只有30萬至50萬。這種差別是保證超高分子量聚乙烯具備足夠的強(qiáng)度,以達(dá)到其他低等聚合產(chǎn)品所不可能具備的耐磨損和抗沖擊能力。
要獲得佳焊縫強(qiáng)度,焊條必須用與基材相 同的 材料制成。 - 典型的 熱氣溫度是350度。半結(jié)晶材料典型的
熱氣溫度是熔點(diǎn)以上80度至100度 - 焊合工具的 移動(dòng)速度通常為0.1至 0.3m/min。焊槍沿著連接軸以鐘擺形式移動(dòng)可以獲得較好的 效果.
- 焊條和焊接零件間的 夾角應(yīng)接近90° - 典型的 氣體流速范圍為16-60升/分. pp板材熱氣焊接工藝方法 使用的
熱氣可以是空氣,或氮?dú)?Nitrogen)等惰性氣體
?。ㄓ糜谘趸╫xidation)降解敏感性材料)。微晶鑄石板極高的分子量賦予其優(yōu)異的使用性能,而且屬于價(jià)格適中、性能優(yōu)良的熱塑性工程塑料,它幾乎集中了各種塑料的優(yōu)點(diǎn),具有普通聚乙烯和其它工程塑料無可比擬的耐磨、耐沖擊、自潤(rùn)滑、耐腐蝕、吸收沖擊能、耐低溫、衛(wèi)生無毒、不易粘附、不易吸水、密度較小等綜合性能。事實(shí)上,目前還沒有一種單純的高分子材料兼有如此眾多的優(yōu)異性能。氣體以及零件
必須干燥、無灰塵和油脂。零件邊緣在焊前 應(yīng)倒角,或者兩個(gè)零件形成拐角。兩個(gè)零件 均在夾具內(nèi)夾緊,保證其正確位置(position )。熱氣焊
一般是手工操作。焊工一手持焊接工具,另一只手則將焊條壓 入焊縫區(qū)。很顯然焊縫質(zhì)量非常依賴于焊工 的 技巧。使用底片或滾子改裝的 焊接工具,
通過增加對(duì)焊接壓力的 控制,可以提高焊接 速度和質(zhì)量. 聚丙烯(PP)板,(PP純板,改性PP板,增強(qiáng)PP板,PP焊條)
純PP板:密度小,易焊接和加工,具有優(yōu)越的
耐化性,耐熱性及耐沖擊性、無毒、無味是目前符合環(huán)保要求之工程塑料之一。主要顏色有白色,微機(jī)色,其它顏色也可按客戶要求定做。應(yīng)用范圍:耐酸堿設(shè)備,環(huán)保設(shè)備,廢水、廢氣排放設(shè)備用,洗滌塔,無塵室,半導(dǎo)體廠及其相關(guān)工業(yè)之設(shè)備,也是制造塑料水箱(組成部分:高水箱、存水箱、低水箱)的
首選材料,其中PP厚板材廣泛用于沖壓板,沖床墊板等。
聚丙?。≒P)擠出板材是PP樹脂添加入各種功能助劑經(jīng)擠出、壓光、冷卻、切割等工藝過程而制成的 塑料板材。
PP板是一種半結(jié)晶性材料。它比PE要更堅(jiān)硬并且有更高的 熔點(diǎn)。由于均聚物型的 PP溫度高于0℃以上時(shí)非常脆,因此許多商業(yè)的
PP材料是加入1~4%乙烯的 無規(guī)則共聚物或更高比率乙烯含量的 鉗段式共聚物。共聚物型的 PP材料有較低的
熱扭曲溫度(100℃)、低透明度、低光澤度、低剛性,但是有有更強(qiáng)的 抗沖擊強(qiáng)度(strength)。PP的 強(qiáng)度隨著乙烯含量的
增加而增大。PP的 維卡軟化溫度為150℃。由于結(jié)晶度較高,這種材料的
表面剛度和抗劃痕特性很好。PP不存在環(huán)境應(yīng)力開裂問題(Emerson)。通常,采用加入玻璃材質(zhì)纖維、金屬添加劑或熱塑橡膠的
方法對(duì)PP進(jìn)行改性。PP的 流動(dòng)率MFR范圍在1~40。低MFR的 PP材料抗沖擊特性較好但延展強(qiáng)度較低。對(duì)于相同MFR的 材料,共聚物型的
強(qiáng)度比均聚物型的 要高。由于結(jié)晶,PP的 收縮率相當(dāng)高,一般為1.8~2.5%。并且收縮率的 方向均勻性比PE-HD等材料要好得多。加入30%的
玻璃添加劑可以使收縮率降到0.7%。均聚物型和共聚物型的 PP材料都具有優(yōu)良的
抗吸濕性、抗酸堿腐蝕性、抗溶解性。然而,它對(duì)芳香烴(如苯(化學(xué)式:C6H6)
)溶劑、氯化烴(四氯化碳)溶劑等沒有抵抗力。PP也不象PE那樣在高溫下仍具有抗氧化性
本文鏈接:
/index.php?c=show&id=245
相關(guān)文章
點(diǎn)擊次數(shù):0更新時(shí)間:2022-05-25【打印此頁】